高效的企业现场管理是实现生产力和质量跃升的关键,而6S管理正是这一目标的基石。它通过系统化的方法优化工作环境,激发员工潜力,为企业创造可持续的竞争力。以下是其核心要素与实践路径的深度解析。
一、6S管理的起源与核心理念
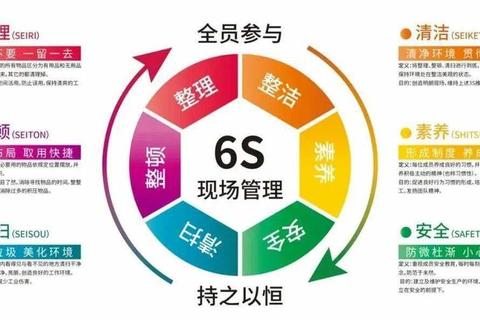
起源于日本制造业的5S管理(整理、整顿、清扫、清洁、素养),在20世纪80年代引入中国后,结合安全生产需求新增“安全”要素,形成如今的6S框架。其核心理念在于通过环境改造推动行为规范,最终实现效率提升与文化塑造的双重目标。例如,丰田汽车通过5S管理优化生产线布局,将设备故障率降低30%,成为精益生产的典范。
二、6S管理的六大核心要素解析
1. 整理(SEIRI)
目标:消除空间浪费,提升资源利用率。
操作建议:
制定物品分类标准(如必需品、非必需品、待处理品),通过“红牌作战”标识冗余物品。
定期清理过期物料,避免仓储积压。例如,某医疗器械企业通过整理工具柜,将设备取用时间缩短40%。
2. 整顿(SEITON)
目标:实现物品可视化与流程标准化。
关键技巧:
采用“三定原则”(定点、定容、定量),如使用颜色标签区分工具类别。
设计目视化管理看板,实时更新生产进度。某汽车零部件厂通过整顿生产线,搬运距离减少60%。
3. 清扫(SEISO)
目标:预防隐患,保障设备稳定性。
实践案例:某食品工厂建立设备点检表,每日记录润滑与清洁状态,设备故障率下降25%。
4. 清洁(SEIKETSU)
目标:建立长效维护机制。
实施策略:
制定清洁标准手册,如地面无尘级别、设备擦拭频率等。
引入数字化巡检系统,自动记录执行情况并生成改善建议。
5. 素养(SHITSUKE)
目标:培养自主管理意识。
提升路径:
通过“改善提案制度”鼓励员工参与,如某电子厂员工年度提案达2000+条,节省成本超百万。
开展6S知识竞赛,强化行为习惯。
6. 安全(SECURITY)
目标:构建零事故工作环境。
关键措施:
标识危险区域(如高温设备、化学品存放区),设置应急处理流程图。
定期模拟消防演练,某化工企业通过安全培训,事故率下降75%。
三、6S管理的实施路径与实用工具
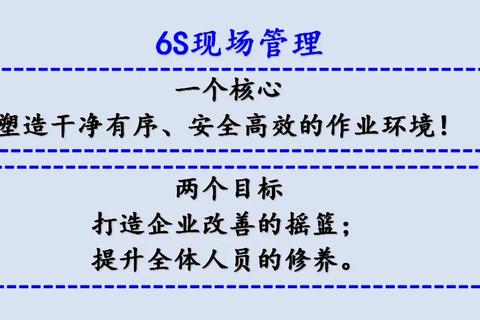
1. 四阶段推进法
准备阶段(1-2个月):成立跨部门推进小组,制定目标与考核指标。例如,某制造企业将6S与KPI挂钩,管理层绩效占比30%。
试点阶段(2-3个月):选择样板区(如仓库或车间)优先突破,通过前后对比照片激发全员信心。
全面推广(3-6个月):建立区域责任制,如“责任田”划分到班组,每日5分钟巡查。
固化阶段(持续优化):每月举办“6S成果发布会”,分享最佳实践。
2. 五类工具提升效率
目视化管理:使用标签、看板、指示灯等直观展示信息。
PDCA循环:通过“计划-执行-检查-改进”持续优化流程。
数字化系统:如智能巡检APP实时追踪问题整改。
红牌作战:对不符合项贴红牌,限时整改并公示结果。
5W1H分析法:针对问题根源制定对策(Why-What-Where-When-Who-How)。
四、跨行业应用场景与挑战应对
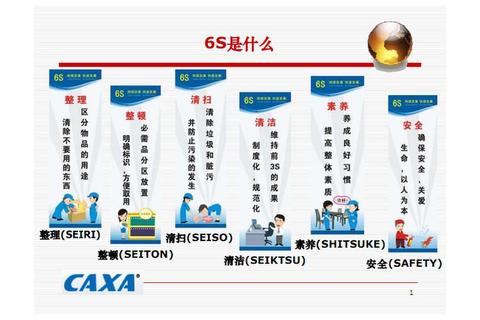
1. 制造业:优化生产线布局,减少物料搬运浪费。某服装厂通过U型生产线设计,人均效率提升18%。
2. 医疗行业:规范药品存储,采用色标管理避免交叉感染。某三甲医院通过6S管理,器械准备时间缩短50%。
3. 服务业:银行网点通过文件分类归档,客户等待时间减少30%。
常见挑战与对策:
员工抵触:通过“改善周”活动展示短期成果,如某车间首周清理3吨废料,腾出200㎡空间。
执行反弹:设立“6S积分制”,兑换奖励(如休假或培训机会)。
资源不足:优先改造高价值区域,分阶段投入预算。
五、未来趋势:从现场管理到文化基因
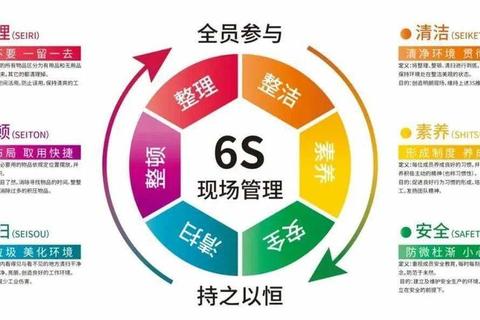
随着数字化转型,6S管理正与物联网、大数据融合。例如,智能传感器实时监测设备状态,AI算法预测安全隐患。ESG(环境、社会、治理)理念的兴起,推动6S向绿色管理延伸,如某新能源企业将“碳足迹追踪”纳入清洁标准。
6S管理不仅是工具,更是企业文化的载体。其成功的关键在于全员参与、持续改进、与业务深度融合。正如某企业家所言:“6S的终点不是整洁的现场,而是员工眼中对卓越的追求。”通过系统规划与务实执行,企业将实现从效率到竞争力的全面突破。