在制造业中,QC质检员是确保产品从原材料到成品的每一环节都符合标准的关键角色。他们如同产品质量的“守门人”,通过严谨的检验流程和专业判断,维护企业信誉与消费者权益。本文将深入解析QC质检员的核心职责、质量检查全流程,并结合实际场景提供实用建议。
一、QC质检员的角色定位与核心职责
QC(Quality Control)即质量控制,质检员的核心职责是通过系统化的检验手段,识别并消除生产过程中的质量风险。根据岗位分工,QC可分为四大类:
1. IQC(来料检验)
职责重点:对外购原材料、零部件进行检验,确保符合采购要求。
关键动作:核对物料规格、抽检性能指标(如尺寸、外观、化学成分)、记录检验结果并处理不合格品。
实用工具:卡尺、千分尺、光谱分析仪等。
2. IPQC(过程检验)
职责重点:监控生产流程,确保工艺参数、设备状态和操作规范符合标准。
关键动作:首件检验、巡检工艺执行情况、记录异常并督促整改。
常见场景:发现设备参数偏移时,立即停机调整并追溯问题批次。
3. FQC(成品检验)
职责重点:对完成所有工序的产品进行最终质量验证。
关键动作:全面检测外观、功能、安全性,确保符合出厂标准。
典型案例:电子产品需通过高低温测试、跌落试验等模拟极端环境下的性能。
4. OQC(出货检验)
职责重点:在发货前对包装、标签、批次信息进行复核。
关键动作:抽样检查包装完整性,核对客户订单要求,避免错发漏发。
风险防控:发现标签错误时,需全批次返工并升级至质量主管决策。
二、质量检查全流程详解
QC质检员的工作遵循“预防为主,检验为辅”的原则,流程可分为以下阶段:
1. 来料检验(IQC)流程
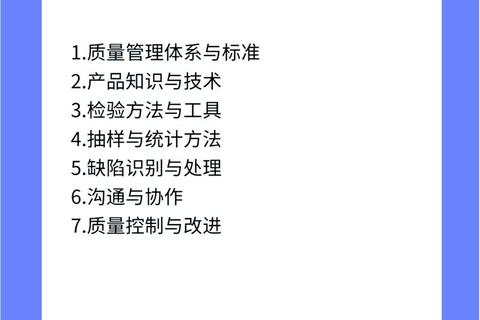
步骤:
1. 接收供应商送货单,核对物料名称、数量与订单一致性。
2. 按抽样标准(如AQL水平)抽取样本,进行外观、尺寸、功能检测。
3. 判定结果:合格品入库,不合格品标记隔离并通知采购部门处理。
常见问题:供应商以次充好时,需启动让步接收评审程序,评估风险后决定是否特采。
2. 生产过程监控(IPQC)流程
步骤:
1. 首检确认:每批次生产前检查首件产品是否符合工艺图纸。
2. 定时巡检:每小时记录设备参数(如温度、压力)、操作规范性。
3. 异常处理:发现偏差时,开具《纠正措施单》并跟踪整改效果。
实用技巧:使用QC七大手法(如柏拉图分析不良主因,鱼骨图追溯问题根源)提升效率。
3. 成品检验(FQC)与出货控制
步骤:
1. 全性能测试:例如汽车零部件需通过耐久性、疲劳强度试验。
2. 数据归档:将检验记录输入质量管理系统,生成可追溯报告。
3. 出货放行:确认检验报告、包装标识无误后签发《合格证》。
风险案例:某食品企业因漏检包装密封性导致运输中变质,损失超百万。
三、QC质检员的常见挑战与应对建议
1. 平衡效率与质量
问题:生产部门追求产量,可能忽视质检要求。
解决策略:
建立跨部门质量目标考核,将漏检率纳入生产团队绩效。
采用自动化检测设备(如视觉识别系统)提升检验速度。
2. 处理供应商争议
问题:供应商对不合格判定结果不认可。
解决策略:
保留检验影像、第三方检测报告作为证据。
定期与供应商开展联合评审,统一检验标准。
3. 应对突发质量问题
问题:客户投诉产品存在隐性缺陷。
解决策略:
启动8D报告流程:从问题、临时遏制措施到根本原因分析。
建立质量案例库,避免同类问题重复发生。
四、提升QC工作效能的实用工具与培训建议
1. 推荐工具
数据分析:使用Minitab进行SPC(统计过程控制),识别过程波动趋势。
文档管理:通过ERP系统实现检验记录电子化,减少人为错误。
2. 职业发展路径
技能进阶:从基础检验员→质量工程师→质量经理,需掌握ISO9001体系、APQP(先期产品质量策划)等知识。
认证建议:考取注册质量工程师(CQE)、六西格玛绿带证书提升竞争力。
3. 日常习惯培养
记录规范化:每日填写《巡检记录表》,标注异常点与处理结果。
持续学习:关注行业标准更新(如汽车行业的IATF16949),参与内部培训。
QC质检员的工作远不止于“挑毛病”,而是通过科学的方法和系统的流程,为企业构建质量防线。无论是新入行的检验员,还是资深质量管理者,都需以数据驱动决策,在标准化与灵活性之间找到平衡。只有将质量意识渗透到每个环节,才能真正实现“零缺陷”的目标,推动企业与行业共同成长。